Patients at Emergency Pharmacy laud innovative flag labelling system on bottles
17 August 2015, Singapore: KK Women's and Children's Hospital (KKH) has rolled out a new robotic bottle dispensing system (BDS) at its Emergency Pharmacy [which serves the Children's Emergency as well as O&G (24-Hour) Clinic] to enhance efficiency and improve overall patient experience. The system believed to be the world's first automated system able to autoload, pick, assemble and label bottles, replaces many of the manual tasks involved in dispensing bottled medication. It is able to pack close to 100% of all bottled medications required at the Emergency Pharmacy. The system also features yet another industry first, an innovative flag label that enables patients to read the original medication labels on the bottles and reference drug facts and ingredients.
Previously, staff at the Emergency Pharmacy had to manually pick, pack, assemble, barcode, and track expiry dates and batch numbers, across various types of bottled medication. About 8,760 man-hours are invested in these tasks a year. Implemented since March 2015, the new robotic BDS has replaced many of these manual tasks which are time-consuming and labour-intensive, allowing pharmacy staff to dedicate their time towards duties requiring more of their expertise, such as performing drug accuracy checks which enhances patient safety. It also allows them to focus on other key aspects of holistic patient care, such as establishing better communication about the drug prescription and rapport with patients.
The BDS is part of the Outpatient Pharmacy Automation System (OPAS) which is a total automated solution for the entire medication dispensing workflow at KKH's Emergency Pharmacy. Working alongside an existing conveyor system, the BDS taps on radio frequency identification (RFID) technology to provide an automated drug dispensing, tracking and delivery system. A patient with a prescription first presents a printed copy of his prescription at the Emergency Pharmacy. The pharmacy staff verifies the medication order and scans a barcode located on the prescription to allocate a RFID tag to the patient's unique identifier. The automated system then kicks in to locate and pick out the medication and places them in small baskets which are embedded with an RFID chip stored with the patient's information and prescription. The basket is delivered via the conveyor system to the pharmacy staff who performs an additional round of accuracy check. The pharmacy staff then further advises the patient on his/her medical condition and medication before dispensing the medication to the patient.
The new robotic BDS also features an innovative flag label developed by Pharmacy staff following patients' feedback. Many patients had shared that when the old labels printed with their names, prescribed medication and dosage were placed on the bottles, the labels had prevented them from reading the original medication labels on the bottles to reference drug information. To enhance patient safety, the team developed the flag label, which is water, tear, and scratch resistant and transparent on one side, and is attached to the medication's original packaging. The reverse side of the label has several adhesive spots so that when applied onto the bottle, it will be securely fastened to the bottle. The label can also be easily unfastened to reveal the underlying original label. In the same manner, this can also be refastened back to the bottle. This innovative practical label design is believed to be an industry first.
"The majority of our paediatric patients require bottled medication and given that our Emergency Pharmacy serves the busiest A&E in Singapore, we handle about 1,350 to 1,800 bottles of medication each day. We felt that for the benefit of our patients, we needed to make the process more efficient. Automation has allowed us to fully focus on safety checks and providing more holistic patient care. Since implementation, we have been encouraged by positive feedback from staff and patients. Our staff are happy that they can now spend more time directly addressing patients' needs. Patients too have expressed appreciation to our staff for spending more time to better educate them on the use of their medication and care for their conditions. Many others have also told us that they were impressed by the flag labels and have found it very practical." Said Ms Irene Quay, Chief Pharmacist, KKH.
With improvements observed from the implementation of OPAS, the team went one step further to integrate OPAS with the hospital's Inpatient Pharmacy Automation System (IPAS) which is a centralised medication management system that caters to inpatients. The IPAS-OPAS interface, believed to be a first of its kind among hospitals around the world, was implemented successfully on 2 June 2015. (Please refer to Annex A for the new Pharmacy Automated System).
The new robotic BDS was developed over a period of one year, in collaboration with Integrated Health Information Systems, Getech Automation, Singapore Polytechnic, NCS and the Agency for Science, Technology and Research (A*STAR). The team had also assisted in the integration of the OPAS-IPAS Interface. The entire project was fully funded by Ministry of Health, Singapore.
ANNEXE A
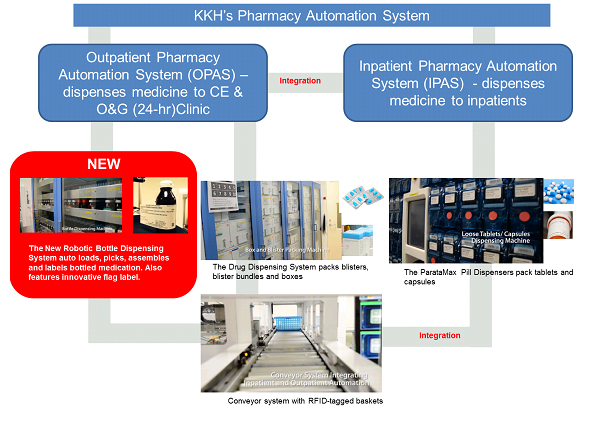