Are you looking for loopholes to meet safety targets?
Is Target Zero Harm just a buzzword? Are you looking for loopholes to meet safety targets? William Lai, safety consultant, wants to have a word with you.
Achieving the goal of zero harm can sound like a colossal task. However, healthcare isn't the only industry giving it a go. Workplace health and safety has been evolving for at least 250 years, and multinational organisations like DuPont and Siemens are notable success stories.
In the oil and gas industry, Shell extends this awareness to its 90,000 staff worldwide, as well as to its vendors and partners.
The goal to achieve zero harm doesn't apply merely to organisations. Even the city of Seattle has a zero harm goal: They aim to end traffic deaths and serious injuries by 2030.A
Like an extension of the Hippocratic Oath "first do no harm", Target Zero Harm can be an achievable destination for healthcare professionals if we all work together.
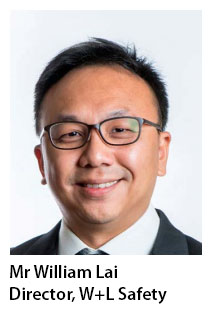
Would you fly on a plane that's 99% safe?
William Lai, founder of W+L Safety – a Workplace Safety & Health consultancy company that helps organisations manage their WSH Management System, helped put this into perspective in a talk titled "Zero Harm in the Workplace".
Held at SNEC Auditorium on 5 October 2017 by the SingHealth Office of Risk Services, William's points were relatable and drew parallels to daily life:
Would you take a flight with an engine that is 99 per cent safe? Would you sign with a telco that has a 15-minute daily disruption? Is it fine to have a daily commute and face five minutes of disruption every day?
The first step to targeting zero harm is as simple as putting ourselves in our patients' shoes - it is only human to hope for the safest and most reliable processes and outcomes.
He was forthright that it is a tough idea to sell to people, but also stressed the importance of recognising that things won't happen overnight.
"People said we were crazy!" William laughed, sharing his own experience in leading another company to take on the new mind set of achieving zero harm.
To begin, he recommended having a simple message that people can envision and be in touch with daily. "It's like creating a brand," he said.
What not to do
There are many ways the concept of zero harm can fall into the conundrum of being just buzz words.
Some wrong ways to achieve "zero" for workplace safety include:
- Cooking the books: In short – not reporting anything, lie and concede that the accident was imaginary and never happened
- Sacking people: If the person involved in the incident doesn't work for you, then he wasn't involved…right?
- Using LTI's (Lost Time Injuries) as a measure: Manipulating LTI can be as simple as getting the injured person to still send in emails or sign work-related forms. In doing that you can keep your LTI's at zero, and still have a Zero Harm Workplace. Never mind the guy is in hospital with broken limbs…
- Hypnosis/Brainwashing: Telling staff to deny what happened: "Nothing happened, it was not an accident, no one got hurt, it was all in your head".
Not doing any work: Any type of work comes with a risk. The only way to achieve absolutely zero harm and be certain that nobody will get hurt is to not do any work.
To avoid the above scenarios, William explained that it is vital to acknowledge that everyone is involved, that not everybody will be a fan, and that management has to come up with a roadmap of definable roles and actions.
Change takes time (What to do)
Moving towards zero harm is a journey and it takes the consistency of bite-sized actions to achieve organisation-wide impact.
Sharing the ideology: Having senior management sprouting a slogan doesn't make zero harm happen. Communicating the message and responding to feedback from the rest of the organisation does.
Everyone knows your action plan: Once a synergised plan has been put into place, it takes an air-tight communications strategy to ensure consistent, constant and concise delivery of the plan to everyone.
Encouraging open discussions: When the whole organisation is talking openly to report and intervene, it becomes a norm to pause and assess risks involved whenever it's necessary.
Creating data: Looking back allows us to move forward. Having a solid base of data that demonstrates the success of your action plan gives everyone the assurance and confidence that we are on our way to zero harm.
He shared that open discussions can be the tough part of the journey, with staff and management needing to be comfortable in doing it. "Managers are very comfortable planning and are knowledgeable, but may lack abilities to engage with the ground."
To work around that, managers can be coached with a script of questions to get to the heart of the risks faced by their team on a daily basis.
Least but not least, William highlighted, "Every time there is a small success, we celebrate it. This continues to encourage people."